Research & Development
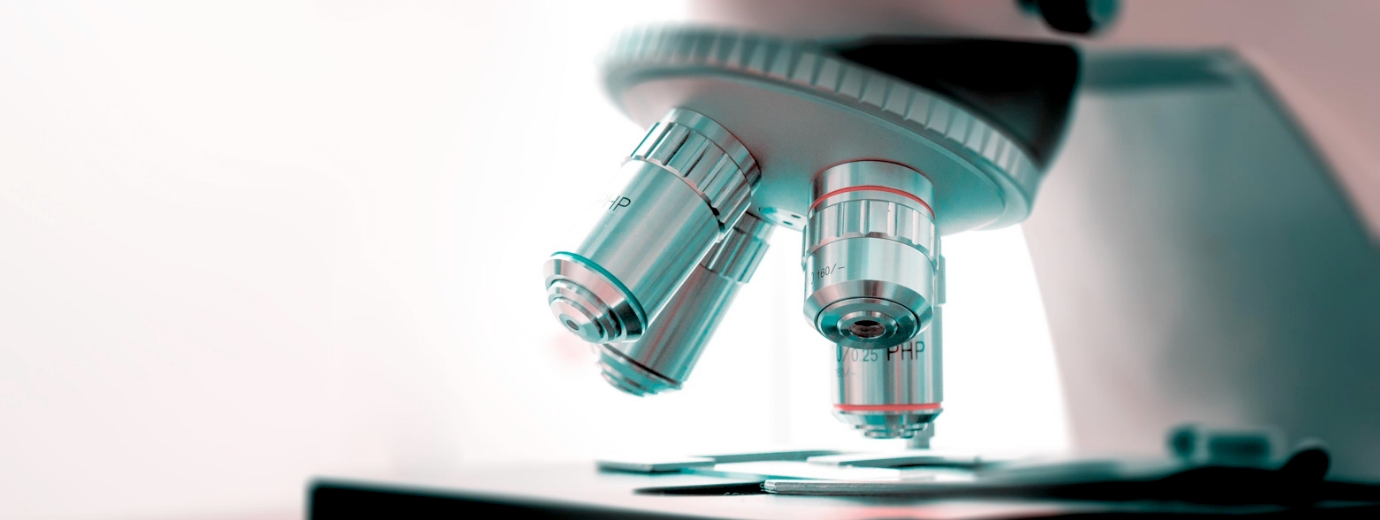
Research & Development Policy
As the world moves toward achieving the Sustainable Development Goals (SDGs), the demand for clean energy applications, especially for environmental conservation, is increasing every year. We will promote product development with a focus on metal ceramic substrates, which are at the core of those applications. Based on our advanced bonding and material technologies, we will actively conduct joint research and development not only within our company and group, but also with companies, customers, and universities both in Japan and abroad in order to introduce superior products to customers.
Research & Development Organization
Our strength lies in our superior research and development capabilities that allow us to introduce high-quality products to customers. We have established an original joint research organization in collaboration with global companies in Germany, the USA, and other countries, as well as with universities in Japan and abroad.
Development Department
- New Development Section
- Searching for new bonding technologies that will lead to next generations developing materials, and searching for new designs and process technologies.
- Product Development Section
- Developing new aluminum metalized substrates and improving the characteristics of aluminum-metalized Integrated Substrates
Engineering Department
- Engineering Section
- Improving the characteristics of and developing new copper metalized substrates
Evaluation Technology for Advanced Research & Development
- Bonding quality evaluation
- C-SAM (C-mode Scanning Acoustic Microscope), transmission x-ray inspection, shear strength test, peel strength test, cross-sectional observation & analysis
- Electrical performance evaluation
- Insulation resistance measurement, dielectric withstand test, Voltage-time characteristics test, partial discharge measurement, electrical conductivity measurement
- Mechanical properties & reliability evaluation
- Material strength evaluation, thermal cycle test, thermal shock test, constant temperature and humidity test
- Shape & dimensions evaluation
- Optical dimension measurement, 3D shape measurement
- Assembly evaluation
- Wire bondability evaluation, solderability evaluation, ultrasonic welding test, laser marking & code readability test
- Morphological observation & material evaluation
- Optical microscope, confocal laser scanning microscopy, SEM-EDX, WDX-XRF, XRD, TG-DTA, Vickers hardness test
- Technical drawing
- 2D CAD,3D CAD
- Simulation
- Thermal stress analysis, heat transfer analysis, thermal-fluid Analysis, casting process simulation, CALPHAD
Major Achievements and Awards
Development achievements (examples)
- Development of "molten aluminum direct bonding"
- We developed "molten aluminum direct bonding," which results in higher bonding yield, higher strength and higher heat dissipating properties than the bonding methods of our competitors.
- Development of "aluminum-metalized Integrated Substrates"
- We developed "aluminum-metalized Integrated Substrates," a one-of-a-kind product that integrates an insulating substrate, aluminum base, and heat dissipating fins into a single unit.
Awards
- 2017.Sept.
Technical Development Award, The Japan Institute of Metals and Materials - [Implementing organization]
(Public Interest Incorporated Association) The Japan Institute of Metals and Materials - [Awarded technology]
Development of aluminum Integrated Substrates for power modules - 2021.Mar.
Technical Skill Award, The Japan Institute of Metals and Materials - [Implementing organization]
(Public Interest Incorporated Association) The Japan Institute of Metals and Materials - [Awarded technology]
Development of aluminum and high thermal conductivity ceramic Integrated Substrates
Research & Development History
- 1985
-
Began research on DBC (direct bonded copper) alumina substrates.
Started shipping samples of DBC (direct bonded copper) alumina substrates.
- 1987
Began research on AMB (active metal brazed) aluminum nitride (brazing method) substrates.
- 1993
-
Began mass production of DBC (direct bonded copper) alumina substrates for industrial applications.
- 1994
Began research on ALMIC substrates (molten aluminum method).
Developed a brazing method.
- 1995
Began mass production of AMB (active metal brazed) aluminum nitride (brazing method) substrates for industrial applications.
- 1996
Developed AMB (active metal brazed) aluminum nitride (brazing method) substrates with fillet for stress relief.
- 1997
Began mass production of ALMIC substrates (molten aluminum method) for automotive applications.
- 1998
Began mass production of AMB (active metal brazed) aluminum nitride (brazing method) substrates with fillet for stress relief for traction applications.
- 2001
Began mass production of thin DBC (direct bonded copper) alumina substrates for industrial applications.
- 2003
Began mass production of alloy-type ALMIC substrates (molten aluminum method) for automotive applications.
- 2007
Began mass production of alloy-type ALMIC substrates (molten aluminum method) for traction applications.
- 2011
Began mass production of Integrated Substrates (molten aluminum method) for new energy applications.
- 2014
Began mass production of thin AMB (active metal brazed) aluminum nitride (brazing method) substrates for industrial applications.
- 2016
Began mass production of Integrated Substrates (molten aluminum method) with cooling fins for automotive applications.
- 2017
Developed partial discharge improvement, developed electroless partial silver plating, established pure aluminum crystal refining technology, established bonding warpage control technology.
- 2018
Established manufacturing process for large-size substrates, established manufacturing process for 0.8 mm copper metallization.
- 2020
Developed new Integrated Substrates (molten aluminum method).
- 2021
Began mass production of aluminum-metalized Integrated Substrates (molten aluminum method) for traction applications.
For inquiries about our product, please contact our sales department of DOWA METALTECH Co., Ltd.
CONTACT
DOWA METALTECH Co., Ltd.
Thermal Device Business Unit
TEL:03-6847-1258
FAX:03-6847-1261